Principle & advantages of MULTICRACKER®
Highly efficient machines providing up to 80% energy saving
The MULTICRACKER® principle
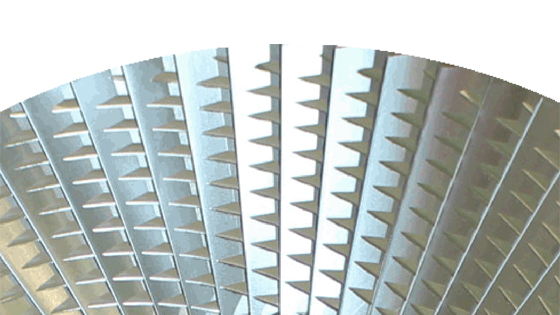
Sophisticated grinding unit
The outstanding characteristics of MULTICRACKER® are based on its innovative and patented grinding unit – the crackerunit with special crackerdisks
Housed in a clearly structurized and standardised machine frame. Idea, design and manufacturing "Made in Germany".
Patented crackerunit
The machine design and the patented crackerunit makes the MULTICRACKER® the perfect machine for your applications.
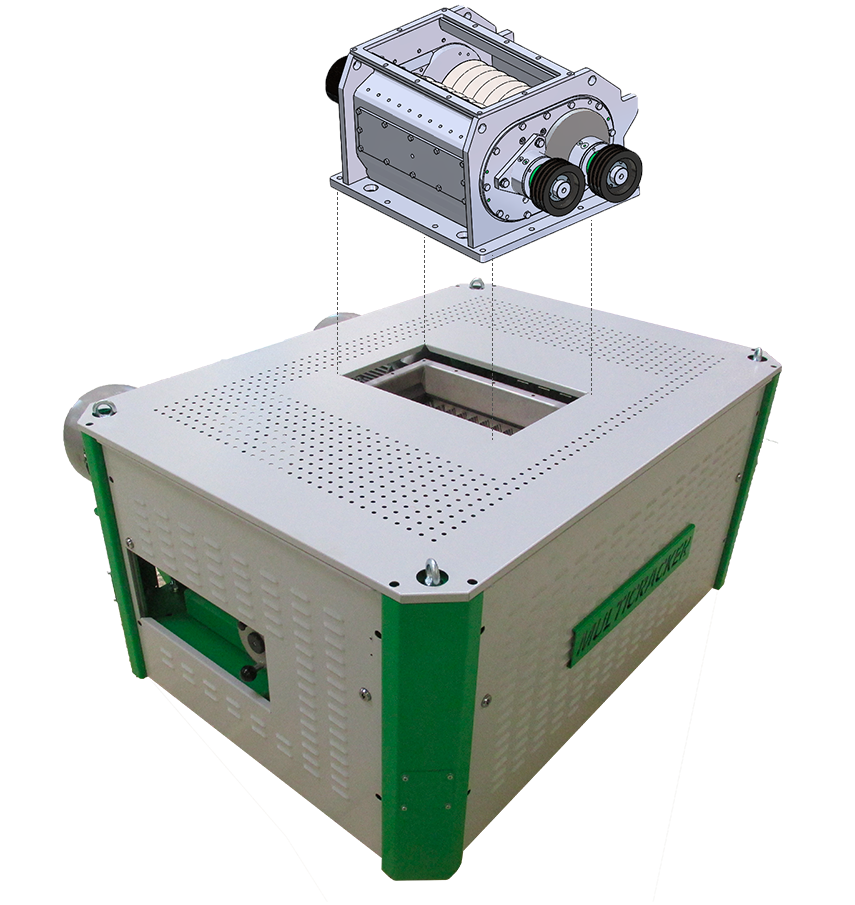
Crackerdiscs
The core of the MULTICRACKER® machines are the unique conical discs made of a special hard alloy that is highly wear resistant.
Cracker unit
The alignement of the conical crackerdiscs on the two shafts inside the crackerunit increases the length of the working gap and hence the capacity about factor three compared to a roller mill with the same dimensions.
Cracker shafts
The cracker shafts are mounted movable and spring loaded inside the crackerunit and allow hard impurities of the raw material through the machine without causing any serious damage.
Gap adjustment
The working gap of the MULTICRACKER® machines is continuously adjustable.
Drivetrain
The machines are driven with one or two motors. The power transmission to the crackerunit is done by v-belts.
Housing
The machines are delivered in powder-coated sheet metal housings in the default colors green (RAL 6018) / light gry (RAL 7035). Individual colors and stainless steel options are available.
Input / Output flange
The machine consists of an input and an output flange for the mill material.
Machine base
The machine base are executed either as welded structure or the are made of high performance reinforced concrete in order to support operation with a minimum amount of vibration.
-
Crackerdiscs
The heart of the MULTICRACKER® machines are the unique cone-shaped cracker discs made of an extremely hard steel alloy which is also highly wear resistant. By bringing in cutting spirals on the conical section of the cracker discs the intake behavior is excellent, analog to the cut by a pair of scissors. Crushing the material this way requires less force and energy input compare to cutting by knifes and much less compare to conventional mills. A similar technique is used by the Great White Sharks to quickly and safely kill its prey. Depending on the design of the profile, they can not only cut but also defibrate, separate, homogenize, granulate, flaking and also agglomerate.
-
Cracker unit
The arrangement of the conical cracker disks mounted on two cracker shafts (so-called crackerset) inside the cracker unit increases the length of the grinding gap and thus the capacity by a factor of 3 compare to a roller mill with the corresponding roller length. Moreover, much lower bearing loads occur due to the fact that the axial and radial forces neutralize each other. The cracker unit can be quickly removed from the machine as a whole and replaced by a spare or resharpened unit. Optional stainless-steel cracker units are available, on demand prepared for "Cleaning-In-Process" (CIP) to meet highest standards in hygienics and corrosion resistance in the food industry.
-
Cracker shafts
The cracker shafts are movably mounted in the crackerunit and pre-stressed fixed using spring packs. This allows both a precise stepless setting of the grinding gap, as well as a foreign object protection by moving the cracker shafts apart from each other hence let foreign objects larger than the grinding gap pass harmlessly. For more versatility, instead of a cracker set rollers or crusher can be used.
-
Gap adjustment
The grinding gap of the MULTICRACKER machines can be set steplessly. This is done by positioning the cracker shafts in the cracker unit manually by handwheel as standard or optionally motorized, controlled by PLC.
-
Drive
The machines are driven by either one or two motors. The power transmission is carried out by V-belts. Therefor the best decoupling of motors and cracker unit in terms of vibration is given, together with easy and quick installation and removal of the cracker units when it comes to servicing. ATEX-compliant motors, along with the ATEX-certified grinding unit allows the operation even in sensitive environments. For the North-American market NEMA-certified motors are available as well.
-
Machine housing
As standard the machines are equipped with a colour coated steel housing green (RAL 6018) and light gray (RAL 7035). Housing panels can be easily unmounted/mounted to provide good and fast accessibility of the machine inside components. For applications with high hygienic requirements, stainless steel housings are available as well.
-
Input/Output chutes
The machines have inlet and outlet chutes for the material to be ground. Apart from standard dimensions, customized sizes and/or stainless-steel chutes are available.
-
Machine base frame
The machine base frames are made either as welded steel structures or cast in high performance reinforced concrete in order to provide operation with a minimum amount of vibrations.
Your advantages
- Highest energy efficiency – energy expenditure ~1 kW per ton - up to 80% energy saving compare to conventional grinding technologies
- Cold cut - no material heating - provides gentle and efficient processing of valuable materials
- Homogeneous grist, narrow grain size Distribution and less dust generation compare to conventional grinding technologies
- Wet grinding and Clean-In-Place possible in water proof crackerunits
- Wide range of applications with various crackerdisk profile
- Dust proof Cracker Units provide ATEX/NEMA compliance
- Small space requirement and weight combined with high throughput
- Low wear-out costs – only 0,10 € per ton
- Low aspiration demand – more energy/cost saving
- PLC-intergrability into new or existing control systems
- Best intake behaviour due to the tapered disks and their formation
Comparison MULTICRACKER® vs. roller mill
- modern vs. tradition
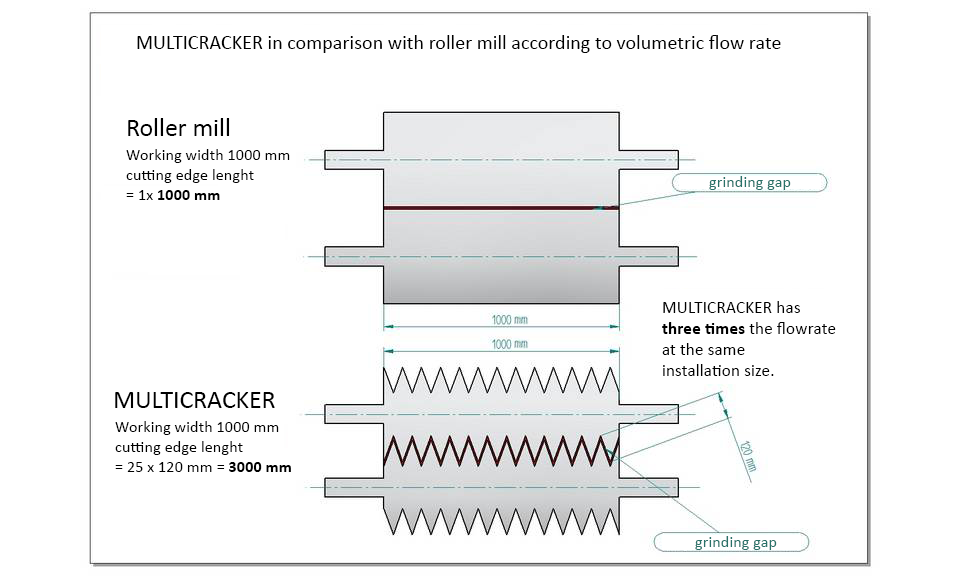
Award winning technology
- Due to its innovative technology and unique advantages MULTICRACKER® was repeatetly awarded:
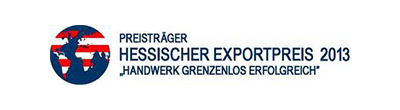
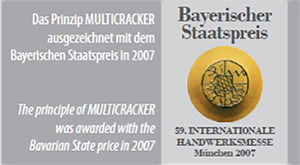
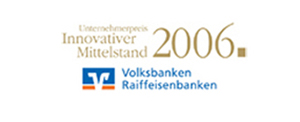